What is DC Sputtering? What is RF Sputtering?
Difference between DC Sputtering and RF Sputtering?
Introduction
Sputtering is the mechanism used to deposit thin films of target material onto a substrate. This process involves ejecting gaseous ions into the source material, thus sputtering gas atoms, ions, and molecules out from the target surface. These emitted particles contain certain kinetic energy, allowing metal ions to increase surface mobility.
This guide below will provide a comprehensive overview of DC sputtering, RF sputtering, Difference between DC Sputtering and RF Sputtering; How these sputtering works etc...

What is DC Sputtering
DC Sputtering (or Direct-Current Sputtering) is a thin-film physical vapor deposition coating technique that uses a direct current as a power source. DC sputtering offers numerous advantages for metal deposition. It’s popular in many manufacturing processes, such as creating metalized packaging plastics and metal coatings on watches and jewelry.
DC or Direct Current Sputtering is a Thin Film Physical Vapor Deposition (PVD) Coating technique where a target material to be used as the coating is bombarded with ionized gas molecules causing atoms to be “Sputtered” off into the plasma. These vaporized atoms are then deposited when they condense as a thin film on the substrate to be coated.
Direct current (DC) sputtering is a thin film deposition technique that uses ionized gas molecules to vaporize (sputter) molecules off the target material into plasma. DC sputtering is the preferred technique for electrically conductive target materials because of its low cost and high level of control globally.

What is Direct-Current Sputtering
The DC magnetron sputtering process involves a vacuum chamber containing the target material parallel to the target substrate. The vacuum chamber contains a high purity inert gas such as argon that becomes charged when exposed to a pulsed DC current.
The metal target material acts as the negative node (cathode) while the substrate acts as the positive pole (anode). A DC current passes through the system, which causes the argon gas to ionize and results in a forceful collision of the ions with the negatively-charged source metal.
These collisions knock off metal ions off the surface of the target into the plasma (a mixture of ionized gas ions and electrons). The positively-charged substrate attracts the negatively-charged plasma, which condenses on the surface of the substrate, forming a thin film coating of the neutral source.
While DC sputtering is a common process for conductive metals, it doesn’t work as well for dielectric target materials. These target atoms can take on a charge, leading to arcing and other disruptions to electron densities, resulting in an uneven deposition rate. The accumulation of these positive ions can even cause the entire sputtering pathway to cease functioning, resulting in the need for a reset.
DC Sputtering Process
DC Sputtering is the most basic and inexpensive type of sputtering for PVD metal deposition and electrically conductive target coating materials. Two major advantages of DC as a power source for this process is that it is easy to control and is a low-cost option if you are doing metal deposition for coating.
DC Sputtering is used extensively in the semiconductor industry creating microchip circuitry on the molecular level. It is used for gold sputter coatings of jewelry, watches and other decorative finishes, for non-reflective coatings on glass and optical components, as well as for metalized packaging plastics.
The basic configuration of a DC Sputtering coating system is the target material to be used as a coating is placed in a vacuum chamber parallel to the substrate to be coated.
The vacuum chamber is evacuated to a base pressure removing H2O, Air, H2, Ar and then backfilled with a high purity inert process gas – usually Argon due to its relative mass and ability to convey kinetic energy upon impact during high energy molecular collisions in the plasma that creates the gas ions that are the primary driving force of sputter thin film deposition. Typical sputter pressures range from 0.5mTorr to 100mTorr.
A DC electrical current is then applied to the target coating material that is the cathode or point at which electrons enter the system known as the negative bias. A positive charge is also applied to the substrate to be coated which become the anode.
The electrically neutral argon gas atoms are first ionized as a result of the forceful collision of these gas atoms onto the surface of the negatively charged target which eject atoms off into the plasma – a hot gas-like state consisting of roughly half gas ions and half electrons that emits the visible plasma glow.
The ionized argon gas atoms are then driven to the substrate which is the anode or positive charged bias attracting ionized gas ions, electrons and the vaporized target coating atoms which condense and form a thin film coating on the substrate to be coated. DC Magnetron sputtering uses magnets behind the negative cathode to trap electrons over the negatively charged target material so they are not free to bombard the substrate, allowing for faster deposition rates than before.
The magnetic field forms a boundary “tunnel” which traps electrons near the surface of the target that improves the efficiency of the gas ion formation. DC Magnetron Sputtering allows for higher current at lower gas pressure that achieves an even higher thin film deposition rate.
While DC Sputtering is the economical solution of choice for many types of metal coatings, its primary limitation is that non-conducting dielectric insulating materials take on a charge over time which can result in quality issues like arcing, or the poisoning of the target material with a charge that can result in the complete cessation of sputtering.
To overcome these limitations of DC Sputtering, several more complicated technologies have been developed such as RF or Radio Frequency Sputtering, and HIPIMS or High Power Impulse Magnetron Sputtering. RF Sputtering alternates the electrical charge at Radio Frequency so as to prevent a charge buildup on the target or coating material. HIPIMS utilizes a very high voltage, short duration burst of energy focused on the target coating material to generate a high-density plasma that results in a high degree of ionization of the coating material in the plasma.
Despite the relative simplicity of DC Sputtering, it usually has low deposition rates compared to more complicated HIPIMS that is the result of lower plasma densities and higher gas densities.
However, the relative simplicity of the DC Power source compared to RF or HIPMIS Power sources that require much more complicated configuration, cabling and higher energy costs continues to make DC Sputtering the low-cost solution for many types of vacuum metal deposition like gold sputtering and other electrically conductive coatings.

How Does DC Sputtering Work
Like any type of sputtering deposition effect, DC magnetron sputtering requires a vacuum chamber. It also requires DC power, positively charged sputtering gas atoms, a target material, and a substrate.
This is the process DC magnetron sputtering systems use to deposit metal coating materials onto substrates:
1, The target or coating material to be used as the thin film is placed in a vacuum chamber.
2, The vacuum chamber is positioned parallel to the desired substrate.
3, The vacuum chamber removes water, air, hydrogen, and argon with a chamber pressure between 1 and 100 mTorr.
4, The chamber then fills with inert process gas ions, such as argon ions.
5, The system applies a DC voltage to the target surface.
6, The target coating material becomes the cathode, and the substrate becomes the anode.
7, The neutral argon atoms become ionized when they collide with the negatively charged target and then eject into high-density plasma, which is generated through neutralization.
8, The now-ionized gas ions remain in the vacuum and break out the target atoms.
9, The ionized gas molecules drive into the substrate.
10, The positive ions condense and form thin films on the substrate.
The magnetic field traps electrons over the sputtering targets, preventing ion bombardment and increasing the deposition rate.
Altogether, DC magnetron sputtering is a relatively simple technique with a high deposition rate, allowing manufacturers to deposit large quantities of surface materials onto substrates quickly, economically, and effectively. This process is essential in a range of commercial applications, such as depositing films of ZnO on glass substrates.
What is RF Sputtering
RF or Radio Frequency Sputtering is the technique involved in alternating the electrical potential of the current in the vacuum environment at radio frequencies to avoid a charge building up on certain types of sputtering target materials, which over time can result in arcing into the plasma that spews droplets creating quality control issues on the thin films – and can even lead to the complete cessation of the sputtering of atoms terminating the process.
Traditional DC Sputtering is a cost effective way of applying metal target coatings that are electrical conductors like gold. However, DC Sputtering is limited when it comes to dielectric target materials – coatings which are non-conducting insulating materials that can take on a polarized charge. Examples of common dielectric coating materials used in the semiconductor industry include Aluminum Oxide, Silicon Oxide and Tantalum Oxide.
RF Magnetron sputtering uses magnets behind the negative cathode to trap electrons over the negatively charged target material so they are not free to bombard the substrate, allowing for faster deposition rates.
Over time, positive ions are produced which accumulate on the surface of the target face giving it a positive charge. At a certain point this charge can build up and lead to a complete secession of sputtering atoms being discharged for coating.
By alternating the electrical potential with RF Sputtering, the surface of the target material can be “cleaned” of a charge buildup with each cycle. On the positive cycle electrons are attracted to the target material or cathode giving it a negative bias. On the negative portion of the cycle – which is occurring at the radio frequency of 13.56 MHz used internationally for RF power supply equipment – ion bombardment of the target to be sputtered continues.
RF Sputtering offers several advantages depending upon your specific application. RF plasmas tend to defuse throughout the entire chamber rather than concentrating around the cathode or target material as with DC Sputtering.
RF Sputtering can sustain a plasma throughout the chamber at a lower pressure (1-15 mTorr). The result is fewer ionized gas collisions equaling more efficient line-of-site deposition of the coating material.
Because with RF Sputtering the target material is being “cleaned” with each cycle from building up a charge it helps reduce arcing. Arcing is where there is an intensely focused and localized discharge emanates from the target material or cathode into the plasma that creating droplets and problems with non-uniform film deposition. RF Sputtering greatly reduces the buildup of a charge in a specific location on the surface of the target material that leads to the sparks that creates the arc which causes numerous quality control issues.
RF Sputtering also reduces the creation of “Race track erosion” on the surface of the target material. With Magnetron Sputtering, a circular pattern becomes etched into the surface of the target material as a result of the circular magnetic field of the magnetron focusing the charged plasma particles close to the surface of the sputter target. The diameter of the circular pattern is the result of the magnetic field.
With RF Sputtering the width and depth of the race track is much less due to the AC nature of the RF discharge with electrons less confined by the magnetic field. The plasma spreads out more producing a larger, wider and shallower racetrack. This makes for better, more uniform and efficient utilization of target coating materials without the deep etching of “Race track erosion”.
Another advantage of RF Sputtering is that there is no disappearing anode effect when the substrate to be coated becomes insulated and acquires a charge as with DC Sputtering. All surfaces develop a charge in a plasma as a result of electrons moving much faster than ions due to their smaller size and kinetic energy.
However, as a result of the AC modulation of the power at radio frequencies, the material to be coated with RF Sputtering does not acquire as great a charge buildup due to it being discharged each half cycle and becoming insulated – which over time can eventually lead to a cessation of the thin film deposition. With RF Magnetron Sputtering the magnetic field forms a boundary “tunnel” which traps electrons near the surface of the target improving the efficiency of gas ion formation and constraining the discharge of the plasma. In this way, RF Magnetron Sputtering allows for higher current at lower gas pressure that achieves an even higher deposition rate.
What is Radio Frequency Sputtering
While RF Sputtering offers many very attractive benefits depending upon the type of material to be coated, there are several important costs involved that must be considered. Because RF Sputtering uses radio waves instead of DC current, deposition rates are considerably slower with RF Sputtering and require significantly higher voltages.
Radio waves require much higher voltage to achieve the same deposition results as with direct current, and so overheating becomes an issue. Applying RF power is complicated requiring high voltage power supplies that are expensive. Advanced circuitry is required that can pose additional overheating problems.
Another issue is that the RF currents travel on the “skin” or surface of conductors and not through them. This means that special cabling / connectors are critical.
Another major consideration that needs to be factored with RF Sputtering rates is the decrease in deposition rates due to the lack of secondary electrons being trapped above the target as with conventional Magnetron Sputtering for gas ionization. With all types of sputtering, the plasma is sustained by the breakdown and ionization of an inert gas such as argon – which is most widely used due to its larger mass compared to the other inert gasses, helium and neon.
By alternating the current at a high radio frequency, a plasma can be sustained with much lower pressure due to the kinetic energy resulting from accelerating and reversing the electrons for a sufficient distance in the plasma. The difference in the mass between the ionized gas particles and the electrons enables a plasma to be sustained without depending upon the trapping of secondary ions above the target material as with conventional Magnetron Sputtering.
However, this also results in a slower deposition rate compared to DC Sputtering due to the lack of secondary electrons above the target. Because RF Sputtering deposition rates are slower than DC Sputtering rates and have much higher power costs, on a practical level this translates into RF Sputtering usually being used on smaller substrates to be coated.
While RF Sputtering can be used for most types of thin film deposition coatings, it has become the thin film deposition technique of choice for many types of dielectric coatings – insulating coatings which are non-conducting that can take on a polarized charge. RF Sputtering is at the heart of the semiconductor industry producing highly insulating oxide films between the thin film layers of microchip circuitry including Aluminum Oxide, Silicon Oxide and Tantalum Oxide.
So as we can see now, sputter deposition of insulating materials cannot be done with DC power. Materials such as oxides, nitrides, and ceramics have very large DC impedance and require prohibitively high voltages to ignite and maintain a plasma. Luckily, the impedance of these materials changes with the frequency of the applied power. Using power delivered at radio frequencies (RF) and an automatic impedance matching network, the total impedance of the circuit can be regulated to 50 Ω which is suitable for plasma ignition in typical sputtering environments.
The radiofrequency (RF) sputtering process is an evolution of DC sputtering that aims to address unwanted charge build-up that happens with some sputtering target materials. This charge build-up can be very disruptive and may result in quality control concerns during film formation.
RF sputtering alternates the potential of the current in the vacuum environment by using a high-voltage RF source. This alternating current avoids the build-up of charged plasma particles and gas ionization, essentially “cleaning up” the charge build-up after every cycle. If the first cycle uses a negatively-charged target material, the ionized gas ions remain at the anode at the end of the cycle.
The next cycle uses reverse polarization to change the charge on the target and substrate, resulting in positively-charged sputtering gas atoms that move towards the negatively-charged substrate.
The main drawback of RF sputtering compared to pulsed DC sputtering is a significantly lower deposition rate and a much higher power requirement. The deposition rate is improvable with a strong magnetic field along the power source to keep the charged plasma discharge closer to the metallic target surface. The technique also draws a lot of power, which is why most RF power supplies can provide up to 1,000V to generate the correct signal.
Another drawback is that any RF sputtering source needs an impedance matching network between the vacuum chamber and the RF power supply equipment. This network prevents interference from the RF discharge that may reduce the overall sputtering rate.


DC vs RF Sputtering
Direct current sputtering is one of several magnetron sputtering methods. Another is radiofrequency sputtering or RF sputtering.
The primary distinguisher between these two processes is in their applications. DC sputtering is suitable for conductive materials and magnetic materials. However, RF sputtering can deposit conductive and non-conductive materials, such as oxide films.
DC power is also distinct from RF power, impacting the voltage behind the sputtered atoms. Whereas DC sputtering uses a direct charge voltage, RF sputtering alternates charges, necessitating a more complex, expensive manufacturing process.
Although DC and RF sputtering are both sputtering deposition techniques, these processes impact the material morphology of their sputtering targets differently.
One of the primary differences between DC and RF sputtering is their power sources. As the name suggests, DC sputtering uses a direct current as a power source. Meanwhile, RF sputtering alternates its electrical charge to prevent the charge from building up on the target material.
RF sputtering is sometimes known as AC sputtering because of the alternating current within RF power supplies.
DC sputtering also has a higher deposition rate than RF sputtering. While DC sputtering is suitable for depositing large quantities onto large substrates, RF is more effective within smaller substrates.
DC and RF sputtering can deposit different types of target materials. While DC sputtering can deposit electrically conductive target materials, an RF sputtering method is suitable for various sputtering targets, including conductive and non-conductive materials.
Finally, DC and RF sputtering vary in their complexities and price points. DC sputtering is more affordable overall, as it uses less specialized processes. RF sputtering involves a more complex process, yet its versatility and excellent campaign length make up for its high price point.
DC Sputtering Review
• The power source is the Direct Current (DC) type.
• Chamber pressure is usually from 1 to 100 mTorr.
• DC power is usually preferred for electrically conductive target materials as it’s effective and economical. Such as pure metal sputtering targets, Iron (Fe), Copper (Cu), Nickel (Ni).
• It is a simple technique when processing large quantities of large substrates.
• The deposition rate is high for some pure metal sputtering targets.
• The positively charged sputtering gas is accelerated towards the target in DC sputtering, and the ejection of atoms gets deposited on substrates.
RF Sputtering Review
• The power source is AC (Alternating Current). The power supply is a high voltage RF source often fixed at 13.56 MHz.
• RF peak to peak voltage is 1000V and the chamber pressure is from 0.5 to 10 mTorr.
• RF sputtering has a wider range of applications and is suitable for all the materials for conductive and non-conductive materials. However, it is most commonly used for depositing dielectric sputtering target materials.
• The deposition rate is lower compare with DC sputtering.
• It is used for smaller substrate sizes due to the high cost.
• The RF sputtering involves two processes. In the first cycle, the target material is negatively charged. This results in atoms' polarization, and the sputtering gas atoms are attracted to the source, where they knock outsource atoms.
Due to polarization, the source atoms and ionized gas ions remain on the target surface.
• In the second cycle, the target is positively charged. Due to reverse polarization, this causes the ejection of gas ions and source atoms. These ions and atoms accelerated toward the substrate to form deposition.
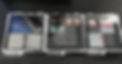